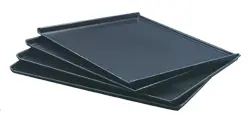
Q: Does it matter what I make Jigs & Fixtures of?
A: Yes … but, before going any deeper, it’s most important to know if the product will have voltage applied to it; the last thing you want to do is either short out any contacts on components or give personnel an electric shock.
When you work with powered product, OH&S prevails.
All too often jigs & fixtures are made of ‘ordinary’, insulating plastics, e.g. Acrylic, PTFE, etc. The problem, as far as static control is concerned, is that these materials are not only capable of generating & retaining a substantial electrostatic charge, but they cannot be grounded.
Example: An isolated, charged (populated) PCB is effectively a charged capacitor that is just waiting to discharge through a component leg via a test probe or tweezers maybe.
By using groundable materials whenever possible, the risk of static generation is reduced … however, this is not always possible.
When groundable materials cannot be used, and when voltage is present, the use of an ionising system should maybe be considered.
As good as ionisers are, implementing them is not always so straight forward, as each application is different & therefore the effects of airflow, obstacles, grounded surfaces, etc. will have an impact on efficiency.
Case study:
During an informal ‘walk-through’ at a client’s facility, we observed a PCB being placed on a test jig. The jig was made primarily of clear acrylic, with an end location incorporating metal pins.
The PCB was slid down the acrylic surface to an acrylic base-stop to square it up. It was then slid along to the end stop, where the metal test-points were located.
As part of the ‘walk-through’ we had a MiniPulse ESD Event Detector at hand. The purpose of which was to detect any ESD events occurring in & around the workshop.
Every time the PCB touched the metal test-points, an ESD event was detected … no surprise really, as the PCB was being charged up all the way along the jig surface & then discharged at the point of contact.
Each application will have a particular set of technical requirements, which will affect the choice of a solution. This could be using conductive / dissipative materials or ionization … or a combination of both. Maybe changing the process to some degree may also need to be considered.